Knurling Tool Holder
Sherline’s knurling tool adds a professional touch to your parts by embossing knurls into the surface, rather than cutting them. Straight knurls are commonly used on the ends of shafts that will be pressed into other parts, while both straight and diamond knurl patterns are ideal for enhancing grip on handwheels and thumbscrews.
This tool can accommodate diameters up to 1″ (25 mm) and features both right and left sides that evenly clamp down on your part as it’s turned in the lathe, creating a consistent knurled pattern. It comes with one set of spiral knurls that form a diamond pattern.
Additional sizes of knurls for both diamond and straight patterns are also available in the addition knurls tab below.
Note: This knurling tool is not intended for use with riser blocks.
-
Body Material | 6061 T6 Aluminum |
---|---|
Body Coating | Black Anodized |
Knurling Wheel Material | High Speed Steel |
Max Diameter Knurling Capacity | 1″ (25mm) |
30561 | (2) 10-32 Tee Nut |
---|---|
36010 | Knurling Holder – Right |
36020 | Knurling Holder – Left |
36030 | (4) .381 x .030 Washer (ID .190″) |
36040 | (2) 3/16″ x 3/4″ Dowel Pin |
3605 | 90-D 20 TPI Spiral Knurls |
40510 | (2) 10-32 x 3/8″ SKT HD Cap Screw |
40520 | (2) 10-32 x 3/16″ Cup Point Set Screw |
40730 | (2) 10-32 x 2″ SKT HD Cap Screw |
40710 | (2) 10-32 x 1-1/4″ SKT HD Cap Screw |
Related products
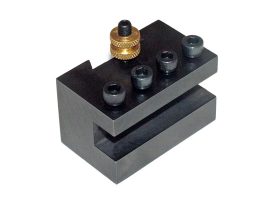
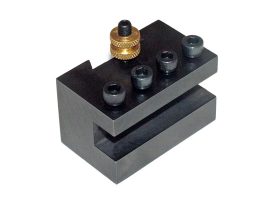
Quick-Change 3/8″ Square Shank Tool Holder


Threading/Grooving Carbide Insert Tool Holder
Due to the variety of insert types and their cost, the holder is sold separately without inserts, allowing you to select only the specific inserts you need. The holder includes a clamp, 6-32 hold-down screw, and a 7/64" hex key for secure setup.
⚠️ CUSTOMER NOTICE — July 8, 2020
We’ve identified a potential issue affecting a small number of our Threading/Grooving Carbide Insert Tool Holders. Specifically, the cutting insert may not be securely clamped in place.
When tightening the clamp, the inside corner of the clamp may contact the step adjacent to the insert pocket, preventing full engagement with the clamping notch on the insert. This was caused by an early in-house clamp design that mistakenly used symmetrical angles on both sides of the clamp nose, rather than the intended asymmetrical design. This issue has since been corrected.
[caption id="attachment_33596" align="alignright" width="300"]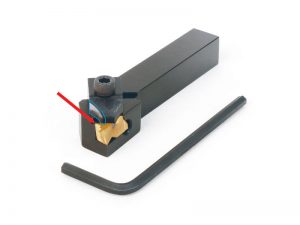
To resolve the issue immediately:
-
Use a bench grinder or file to slightly grind down the back side of the clamp (see blue circle in the image).
-
This will allow the clamp tip to clear the step (indicated by the red arrow), ensuring full contact and proper clamping of the insert.
⚠️ CAUTION: Chips coming off the carbide inserts can be very HOT! Use extreme caution. Carbide inserts can also shatter. For these reasons, proper protective eyewear and clothing are especially important when using these tools. Materials like tool steel can form long, stringy chips that wrap around the part. Use a chip brush frequently, or pause machining to clear debris. Accumulated chips, especially when hot, can ignite. Keep the area around the cutter clean and free of chip buildup.