LH 55° & 80° 3/8″ Boring Bars w/Carbide Inserts
These 3/8″ diameter boring bars hold a carbide insert secured with a Torx screw. Each comes with either a 2-sided 55° or 80° carbide insert and Torx wrench. The 55° LH boring tool will fit into a 3/4″ starting hole. The 80° holder will fit into a smaller 1/2″ hole. The 80° holder offers a little more strength for roughing cuts while the 55° insert will cut into sharper corners. The 3-1/4″ long holder can bore a hole a little over 2″ deep with two fastening screws tightened on it. The holders are made from 1144 Stress-proof steel with a black oxide finish. Available individually.
Left Hand Boring Bars
These LH boring bars are not intended to be used for boring on a standard Sherline lathe, as the spindle is not reversible without electronic modifications. They were developed for a Sherline tool that is now in development where they will be used as a turning tool from the backside with the bit upside down. Watch for the introduction of this new “chucker” lathe soon.
Advantages of Using Carbide Insert Tools
Though relatively expensive, if a cutting edge of a carbide insert becomes dull or chipped, the insert can be removed and rotated 180° to expose two new cutting surfaces, providing, in effect, two tools for the price of one.
The primary method of cutting metal on miniature machine tools is usually with high-speed steel tools as they are inexpensive, easily resharpened and can be ground into “form” tools for special jobs. However, inserted tip carbide tools can be lifesavers for some jobs. Though more expensive and not able to be resharpened, carbide tools hold their cutting edge when cutting exotic metals like stainless steel or titanium or abrasive materials like carbon fiber and can speed up the cutting process. This is why they are used for most cutting tasks in the modern professional machine shop.
NOTE: A tool is named by the direction from which the chip leaves the tool; so a right-hand tool has its cutting edge on the left and the chip peels off to the right.
-
Insert Holder Material | 1144 Stressproof Steel |
---|---|
Body Coating | Black Oxide |
Insert Material | Carbide |
Related products
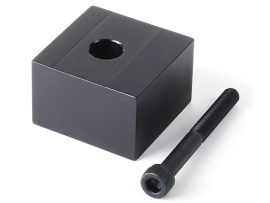
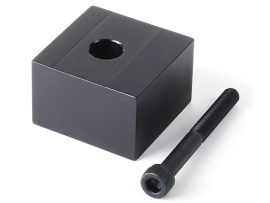
Cutoff Tool Rear-Mounting Block
For those who already own a standard cutoff tool holder, this spacer block will lift the cutoff tool holder the height of the blade, allowing the blade to be mounted upside down and used on the back side of the … Continued
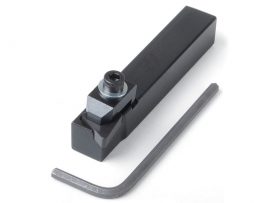
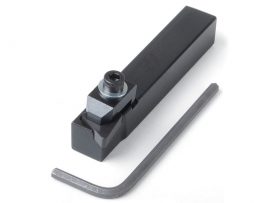
Ceramic Insert Tool Holder
Designed for cutting hard materials like tool steel, this ceramic insert tool holder features a triangular insert mounted at a negative rake angle. The downward tilt of the insert provides proper side clearance, allowing you to use all six cutting edges—three per side—before needing a replacement. The 3/8" shank fits Sherline’s P/N 7600 tool post (not included). A clamp, hold-down screw, and 3/32" hex key are included for secure installation. Replacement inserts are available as (P/N 22659).
Why Use Ceramic Inserts?
Ceramic cutting tools are a powerful addition to the modern machinist’s toolbox. Though more brittle than high-speed steel (HSS) or carbide, ceramic inserts excel at cutting hardened steels and other tough materials, especially at higher spindle speeds. This makes them ideal for jobs that would otherwise be extremely difficult or impossible—such as turning down the shank of an end mill.
This insert’s large nose radius helps achieve an excellent surface finish, particularly when profiling.
-
Each insert offers six usable cutting edges:
-
Rotate 120° to access a new edge (3 per side), then
-
Flip the insert for 3 more cutting points on the opposite face
-
-
In comparison, traditional carbide inserts offer only 2–4 cutting edges, making ceramic inserts cost-effective over time, despite the higher upfront cost.
Usage Notes & Safety Information
-
Ceramic inserts are brittle and should be used with proper technique to avoid chipping or breakage.
-
Caution: Chips produced during cutting can be extremely hot—even red-hot. Use protective eyewear, gloves, and fire-safe clothing when operating.
-
Some materials, such as tool steel, may form long, stringy chips that wrap around the part ("bird’s nest" effect).
Use a chip brush and stop the machine frequently to clear chips. These chip clusters can ignite if they come in contact with hot chips.